Best Resources for Operational Excellence
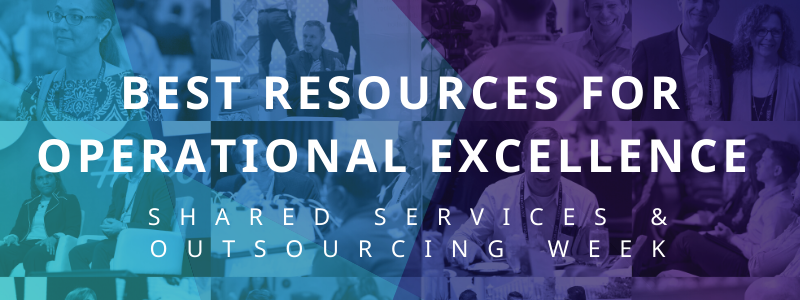
The definition of “operational excellence” defined by Industry Week reads as: “It is when each and every employee can see the flow of value to the customer, and fix that flow when it breaks down.” The goal of every office is to create an environment where employees are able to deliver results that can maintain and obtain customers in the long run. Sometimes it can be difficult to implement a “good office” system simply because “good” can look a lot of different ways to a lot of different companies. Not every principle or model will work in every business let alone every office.
This is why it’s important to focus on the principles of operational excellence, and deciding what sort of environment you need before you ever decide the steps necessary to take you there. Read SSON’s top resources for operational excellence and tools to help you start making changes in your office!
Tallyfy:
This blog post gives you a breakdown on what exactly it takes to excel in operational excellence. Tallyfy lists ten principles that they think a company needs to be able to get the most from their operational excellence. Among these principles is listed, leading with humility, embracing scientific thinking, and creating a constancy of purpose. The key seems to be to create an environment that help your employees envision and enact operational excellence. This Tallyfy blog is also valuable because it lists methodologies, not just principles.
If you’re looking for more practical steps, this list of what they believe the top methodologies are is handy. They include models such as lean manufacturing, sigma six, and kaizen—but tailored specifically from an operational excellence standpoint.
4 Strategies for Operational Excellence:
This article seeks to nail down how companies are using operational excellence, specifically from the perspective of a redesign strategy. “Little is known about the particular strategies that organizations can follow to achieve operational excellence…” The author explains the findings of a university that identified the traits of redesign practices and how those practices worked within varying operational excellence frameworks. They found there to be four types of strategies; “employee-focused”, “cost-focused”, “hybrid” and “workstream-focused.” How well each strategy worked depended on the goals and immediate needs of each firm, but broadly their findings were found to have consistent results and similarities. Read the full article to find out more!
What "Good Looks Like in Process Management:
Having trouble envisioning what “good” looks like in terms of operational excellence? You’re not alone. Bain & Company consulting services released their article about creating a working management system, when picturing the finish line is hard. Fittingly, they open with a quote from Aristotle, the Greek philosopher who tried to explain what exactly “excellence” meant. “Excellence is an art won by training and habituation. We do not act rightly because we have virtue or excellence, but we rather have those because we have acted rightly. We are what we repeatedly do. Excellence, then, is not an act but a habit.”–Aristotle
Using Exxon as a case study, Bain & Company explains OEMS, how to set expectations both close to home and global, define common languages, share successful practices and behaviors, map accountability, and promote continuous improvement.
What resource did you find most useful? Let us know!