RPA Case Study: Establishing Proof of Concept/Ecopetrol
Add bookmark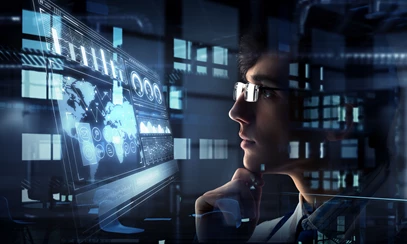
SSON IMPACT AWARDS
In the run-up to the 2019 Impact Awards announcements in North America [March 11 at the 23rd Annual SSO Week Orlando] we are delighted to showcase some of the awards finalists in the "Automation" category, sponsored by Automation Anywhere. First up: Ecopetrol: Finalist in the Automation category.
__________
Ecopetrol, Colombia’s largest integrated oil & gas company and one of the top 40 oil companies in the world, identified process automation as a winning strategy for highly repetitive and manual processes. Over the course of one year, the company implemented 23 bots that automated 13 activities related to portfolio management and collection processes, accounting operation, accounts payable, tax management, personnel benefits management and logistics.
The automation of these activities achieved high impact objectives for the organization, such as:
- Freeing up time for professionals to reinvest in value generation.
- Reducing processing time / increasing the capacity to address additional requests.
- Mitigating risk of human error and ensuring compliance with 100% controls.
- Improving service levels.
- Reducing costs.
RPA was introduced in 2017, by developing two robotic Proof of Concepts (POCs) intended to understand the process and the efforts that would be required, and to identify the automation potential within the organization. Ecopetrol soon realized that RPA would significantly reduce execution times and errors related to human interaction – specifically those associated with the omission of controls, or poor execution thereof. The decision was made, therefore, to integrate RPA in 2018.
From the start, how the message was conveyed by SSC leaders was key, as they generated confidence about the benefits for employees, in terms of freeing up time to generate more value, rather than downsizing. This facilitated the adoption of RPA and generated a high level of commitment to complying with the planned delivery timing.
The implementation of RPA was driven by the SSC team, the digital factory, and supporting consultants, and developed on the Microsoft Azure platform. The initiative was configured as a virtual machine in the cloud. Here are the stages that guided implementation:
1. Planning and Design (Feb/Jun 2018)
-Benchmarking RPA issues with other national companies.
-Defining robotics service model with the Digital Vice President.
-Defining automation success metrics.
-Structuring criteria to evaluate potential process candidates.
-Defining prioritization tool.
-Designing supply strategy to guarantee demand.
2. Socialization and Implementation (Jul/Dec 2018)
- Conceptualization: Socializing concept and criteria of potential processes to robotize with
the SSC areas.
- Applying prioritization tool and defining which robots to build.
- Design: Structuring process flow from the robotic perspective.
- Construction: Creating robot on defined platform.
- Release: Ensuring the technical support documentation required.
- Operation: operation of robot in a productive environment in the stabilization phase.
3. Quantification of benefits, stabilization and continuous improvement (Oct/Dec 2018)
-Customization of benefits according to success criteria defined in design phase.
-Regular validation of compliance with value promise and robot performance.
-DMAIC Assessment of indicator results.
In total, 246 man hours were saved, and redirected to analytics and process control, and processing times were reduced by 20%, resulting in more flexibility for managing service demand. In 2019, bots will generate more than 3000 hours of efficiency and incorporate artificial intelligence / analytics.
Find out who will win this year's Impact Awards in each of the six categories. Join us at Shared Services and Outsourcing Week 2019 – in Orlando.