Digital Transformation in Supply Chain
Add bookmark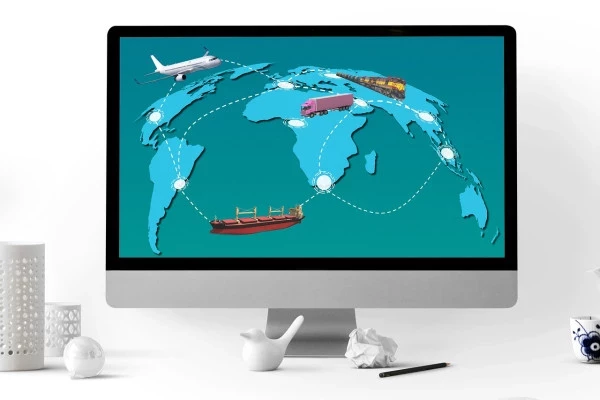
Philips GBS has been recognized as a “Top 20 Most Admired SSOs & GBS” for two straight years and, from time to time, contributes to SSON Digital. In this article, SSON spoke with Rob Van Leuken, Head of GBS Supply Chain for Philips who is responsible for driving process automation and digital transformation across the supply chain as well as service & solution delivery functions for the GBS business.
With the major effects of the pandemic on supply chain and logistics subduing, new geo-political challenges have emerged that are kick-starting another digital revolution in GBS organizations.
At Philips, significant operational transactions are handled through GBS. As a result, Philips GBS has access to a vast array of data that puts them in a unique position to support the parent organization in developing and enabling innovations that improve reliability to customers.
“For example, if we needed to ship into export-controlled regions there are now a lot of steps that need to be taken that didn’t exist in the past to ensure compliance,” said Rob. “Also, for basically every step, there are additional inspections, which has required us to become much more digital in order to coordinate between different functions."
Solutions driving digital transformation
Within Philips, the focus has shifted to greater efficiency through standardization, simplification, and automation of processes. Through the introduction of several digital tools such as E2E dashboards, process mining insights and Robotic Process Automation (RPA), Philips is realizing the initial benefits. For instance, near real-time order life cycle dashboards are allowing visualization of key risks and blocking factors for the order fulfillment team to be resolved, before they can potentially impact a smooth delivery. Key insights are being delivered through the periodical mining of all key SCM data points that when compared to the standard, enables Philips to identify areas for process improvements or automations that were previously unknown.
The benefits that RPA provides have had a positive impact on internal productivity, and when a solution is taking remedial tasks off the hands of employees, it allows them to focus more on their customers. According to Rob, the next step for Philips GBS Supply Chain is further developing ways RPA and hyper automation can directly improve the customer experience.
Creating a digital savvy workforce
With the advent of the digital age, GBS is playing a key role as the provider of RPA solutions that reduce manual effort, improve process accuracy and transactional speed, and data reliability. Becoming more transparent to enterprise stakeholders, listening, and responding to what employees & customers need, and building a future-ready workforce of data and digital experts are key enablers in this journey.
Despite the value in creating a data savvy workforce, one of the biggest opportunities for GBS organizations during their digital transformation efforts is upskilling employees and having a sound change management approach in place to ensure they are comfortable with the new ways of working. Philips GBS is continuously investing in creating more two-way communication opportunities with employees, and building various capability development activities to overcome these challenges.
The expectation at Philips is that their digital transformation initiatives can only strengthen the business if employees are bought in. By shaping these projects to the needs of employees, you are not only ensuring they support digital initiatives, but are being given tools that allow them to focus on more complex tasks and improve the customer experience.
“We’ve made sure to involve experienced people in our organization in any transformation,” Rob said. “It has really been a bottoms-up approach. We simply asked people what their mundane tasks are, where do they think automation can help, and then started to build our RPA efforts around those recommendations.”
Next steps for GBS organizations
Today, GBS organizations can really accelerate digital initiatives and build them out further using AI/ML and automated workflow technology, a journey Philips GBS is currently embarking on as well, and are beginning to see early signs of promise.
“Within the next year we are expecting to see real wins in our digital transformation by looking at productivity and reliability to our customers. And that can be thanks to RPA, integrated data sources, or integrated business processing.” Rob added.
Rob believes this integration between business processes, tools and data is the most meaningful next step for Philips GBS. Once integration is realized, Philips can further improve the standards for workflows, data and business rules that allow supply chain teams to excel at supporting their customers.
Share your feedback on current Supply Chain trends and performance limitations via our Survey:
https://www.surveymonkey.com/r/3N9YHKF