Meeting Local Delivery Requirements in a Global Delivery Model
Add bookmark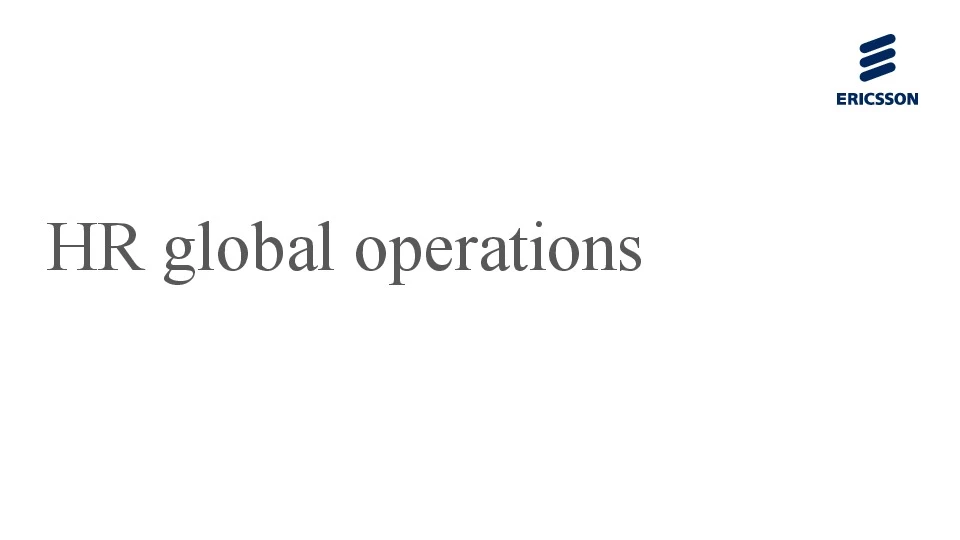
We respect your privacy, by clicking "Download Your Copy" you agree to having your details passed onto the sponsor who may promote similar products and services related to your area of interest subject to their privacy policy. You have the right to object. In addition, you will receive our e-newsletter, including information on related online learning opportunities. For further information on how we process and monitor your personal data, and information about your privacy and opt-out rights, click here.
GLOCAL is the new mantra: Global at the Source and Local as it cumulates.
A key challenge that Global/multifunction/cross-border Shared Services Centers are facing currently is around how to maintain the balance between Global Standardized Delivery, which promotes a “one size fits all” approach and capitalizes on economies of size, scale, and cost; versus taking into consideration the needs of local requirements, which could be internal to organizations or businesses or could be a derivative of the law of the land – often referred to as “internal requirements and regulatory variations”.
This dilemma could be due to a wide variety of factors: Organization size, scope, spread, cost, legacy, stakeholder needs, evolving strategy or business mix etc. … but it presents a challenge for the Delivery Organization: How to solve the changing delivery mix? Should they go for a standard, one size fits all approach? Or should they provide segmentation, on demand delivery, or point solutions?
The choice (and decision) between these two approaches is tough, because both requirements are mutually opposing each other at one end, but mutually contributing to the overall interest of the organization on the other, as the final objective of a Shared Services Center is to meet cost objectives along with customers’ requirements.
Over the course of the years, I have seen that, initially, it is difficult to find this balance but if you have the right strategy in place, this ask is manageable.
We cannot be ready overnight for this, as it requires a fair amount of planning and execution over years before SSCs can adapt to both needs, Global and Local, without losing the essence of SSC, which is cost, speed, efficiency, agility, and standardization.
The first step: Define your maturity journey and delivery model
The following parameters are standard for any SSC, but the time spent in each phase, prioritizing each factor, and using them interchangeably in different phases can be a combination of various factors such as cost, competence of the team, change management, resistance, governance, organizational structure.
- First Phase: Consolidation, Standardization, Simplification, scope clarity, automation/in house technology solutions, change/resistance management
- Second Phase: Partner in decision making, Trending and Analysis, availability of global workflows and tools, moving from transactional to tactical
- Third Phase: Enabling technology, AI and Robotics, moving from Tactical to Strategic
- Fourth Phase: Strategic to Consultative, External benchmarking/getting outside in view
- Fifth Phase: Ability to provide segmentation, on demand delivery, point solutions, and moving to GLOCAL delivery model
[inlinead]
Each organization adapts to each phase differently, in terms of scope, timelines, etc., but side-by-side also tries to maintain a balance between the “business ask” versus “delivery capability”. Also, there are many levers that can be used in each phase.
Over the years we have seen that to manage evolving needs we have to have a fair mix of factory model and customized solutions which can be managed via two frameworks:
DIR Model
Design – Implement – Run Model, where specialist teams concentrate on each facet rather than everyone trying to do everything.
- Design works on creating the process framework and architecture and aligning it with business needs. This function interprets the ask from the customer into delivery requirements.
- Implement works on creating fit to move the process into a Business-as-Usual mode by ensuring all solution components, hands offs, and impact on people, process, and technology are in place
- Run works on delivering the process as per agreed SLAs and KPIs.
Center of Excellence Framework (COE)
One of the essentials for a Global SSC is that it should have a 360-degree view on what is happening in each delivery center, and rather than multiple teams cutting across multiple processes there should be a framework where similar work is performed seamlessly to get the most advantage of spread and knowledge in a GBS/multifunction SSC.
Organizations have achieved considerable success by using these two models (they may be called by different names).
An important point to note is that where SSCs experience changing priorities it will not lead to optimal results (a rolling stone gathers no moss). Basic internal requirements and key strategic pillars should be identified upfront and ongoing investments should be made in them. These pillars will be different in each organization but once identified, they become an integral part of the foundation on which the whole delivery is run. They can be based on governance, spread, domain knowledge, analytical skills, enabling technology, culture, framework, delivery models, etc.
Some of the key wins which can be realized out of DIR and COE models are:
- Design for a truly global SSC at the core, with the ability to handle regional variations
- Better opportunities for workforce in the COE model with the ability to have 360-degree view to problems, solutions, and opportunities
- Ability to share best practices
- Enhanced governance for a geographically spread organization
- Ability to give segmented, on demand and point solutions.
- Ability to administer mass/customized solutions concurrently
- Right workforce mix to handle varied needs
Summary
The key to success is the ability to meet customer requirements on a real time basis and doing things right the first time. This can only be possible when we have a well-oiled machinery which works in a factory model, thereby offering the efficiencies to meet local/ on-demand requirements.
[Note: You can download the presentation that goes with this article below.]